There are currently 53 operational nuclear reactors in Japan: 30 boiling water reactors (BWR) and 23 pressurized water reactors (PWR). Of those, nine (4 BWRs and 5 PWRs) commenced operations more than 30 years ago. In ten years' time, 31 (58%) will have been operating for more than 30 years.
Aging is already a major issue for these reactors and it will become an even more serious concern as time goes by. In this situation there are two possible choices. One obvious choice is to shut them down. The other is to continue to nurse them along.
Metals (mainly iron) make up the majority of the material used in reactors and the surrounding equipment. It is impossible to prevent these materials from degrading with age. Nuclear power plants (NPP) are operated in extreme and complex environments. Judgments about whether to close them or continue operating them rest on how one analyses material degradation. For reasons of cost, nuclear power companies and the Ministry of Economy Trade and Industry (METI) try to operate them for as long as possible. However, citizens are much more concerned about safety than cost. So a strictly neutral scientific and technological judgment is required. Unfortunately, neither the Nuclear Industrial Safety Agency, nor the Nuclear Safety Commission is strictly neutral. Since there is no one in those organizations who is willing to carry out a critical investigation, their judgments are inevitably one-sided.
When cover-ups of damage were revealed at the Tokyo Electric Power Company in August 2002, all 17 of TEPCO's reactors (all BWR) were forced to stop. Two years later, in August 2004, five people were killed and a further six injured in an accident at Kansai Electric Power Company's Mihama-3 reactor (PWR) (see page 8). Both of these incidents were the result of mistaken technical judgments. They nursed them along, all the time covering up or underestimating the problems; and none of the academics, technicians and researchers in the government safety agencies noticed that anything was wrong.
CNIC, being very concerned about this situation, continued to offer a critique of the government's attitude from a scientific and technical standpoint and established a research group to investigate the problems of aging nuclear power plants. Some problems discussed in that research group's recently published report are discussed below.
First, a new riddle has emerged regarding the mechanism of stress corrosion cracking (SCC) of stainless steel. In the 1970s technicians worried about the phenomenon of cracks appearing in stainless steel welds. This problem was solved - it was believed - with the development of stainless steel with a low carbon component. But before long it was noticed that the cracking problem hadn't gone away. It was recognized in the 1990s that the reason for this was a type of SCC which hadn't been noticed previously. It arose as a result of distortion at the time of manufacture and, even though power companies had no solution to the problem, they continued to operate their NPPs, while regulatory agencies turned a blind eye. This came to light when the TEPCO cover-up was revealed. This related to cracks in the reactor shroud and recirculation pipes. As was to be expected, similar problems arose at BWRs operated by other power companies.
This type of cracking begins at weak points in the metal. It proceeds from one crystal grain to the next and is called trans-granular SCC. Previously identified SCC proceeded along the boundaries between grains and was called inter-granular SCC. It is very difficult to discern the shape of these trans-granular cracks using ultrasonic waves and it is impossible to predict the speed at which the cracking will proceed. Technicians whose aim is to keep reactors running use existing models, but since the mechanism involved is different, there is no scientific basis for using these models, so the government's 'fitness-for-service rule' (better termed 'allowable defects standard') can't be relied on.
Second, the Mihama-3 (PWR) accident revealed the phenomenon of carbon steel pipe thinning. The cause of this accident was the fact that the thickness of the pipes went unchecked for many years. The power company and the regulatory agencies failed to notice this. From a scientific point of view the phenomenon of pipe thinning is basically understood. What is not understood, however, is when, where and to what extent the thinning will occur. This is because of the complex conditions associated with the operation of NPPs. It is a technical difficulty. It is very doubtful whether experience and management could ever compensate for this weakness. If the top priority is safety, frequent checks will be necessary. The cost will rise out of all proportions and power companies will abandon nuclear energy.
Third, a problem of particular concern for PWRs is 'pressurized thermal shock' (PTS). This is caused by so-called 'underclad cracking' (UCC). It seems that this occurs at the time of welding stainless steel on the inner walls of the pressure vessel. Under great hydraulic pressure and heat shocks the pressure vessel can be destroyed suddenly. PTS thus has the potential to cause major accidents. Originally the life of nuclear power plants in Japan was thought to be 30-40 years. Now attempts are being made to extend this to 60 years. Consequently, technical investigations are being carried out with a view to developing responses to the problems of aging power plants. However, no scientific or technical investigations are being carried out in regard to UCC. It is being treated as if it was unrelated to aging. But for the five PWRs that have been operating for over 30 years, PTS is a matter of great concern.
In recent years many types of accidents and faults have occurred at NPPs in Japan. In the case of BWRs, there are too many to list in full, but the following are a few examples: damage to fuel rods, cracks in the cladding of fuel rods, cracks in the shroud, cracks in the nozzles of recirculation pipes, cracks in the core spray spurger, fatigue cracking in thermal sleeves, rupture of residual heat removal system pipes, damage and rupture of recirculation pumps, cracks in the control rod drive mechanism tube, thinning of feedwater heater pipes. Much the same could be said for PWRs. For more details, NIT subscribers who read Japanese should read the full report (Roukyuuka suru genpatsu - gijutsu wo tou, CNIC, March 2005). We would like to thank the Takagi Fund for supporting this project and enabling us to publish this report.
Yukio Yamaguchi (CNIC Co-Director)
Note that the schematic diagram of a BWR shown below is riddled with 'x' marks. These show the locations of faults and accidents that have occurred in BWRs.
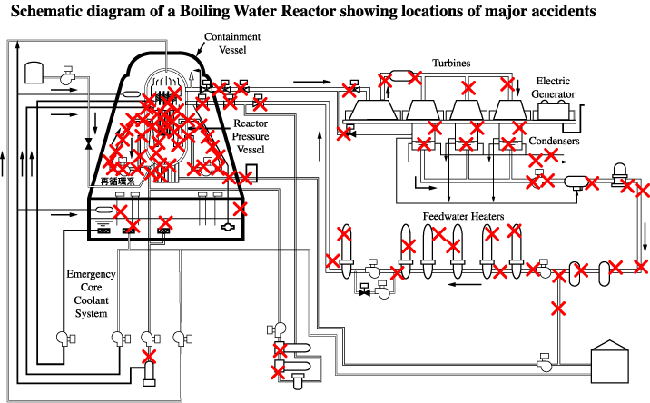
Return to NIT 106 contents